Ransomware Attacks in Manufacturing Doubled From 2019
From 2019 to 2021, ransomware attacks in manufacturing doubled, making it the most commonly targeted industry in 2020 and 2021, according to Advisen loss data. Advisen's loss database contains 3,415 ransomware attacks and 189 ransomware attacks in manufacturing.
The manufacturing industry is a high-value target for ransomware attacks. Most manufacturers have embraced automation and digitization, but many only store files locally, leaving them vulnerable to attack.
Manufacturing companies also store high-value data, such as intellectual property and trade secrets, which makes manufacturers more likely to pay if their information is stolen or hackers threaten to publish it online. In some cases, hackers will steal data involving third parties as well, such as clients, suppliers and partners. This gives them even more leverage to extort money in a ransomware attack.
In addition to ransom payments, ransomware attacks on manufacturing can also be extremely costly in terms of response and business interruption costs. For example, the ransomware attack on meat supplier JBS Foods on May 31, 2021, resulted in a total shutdown of operations and an $11 million ransom, according to Advisen loss data.
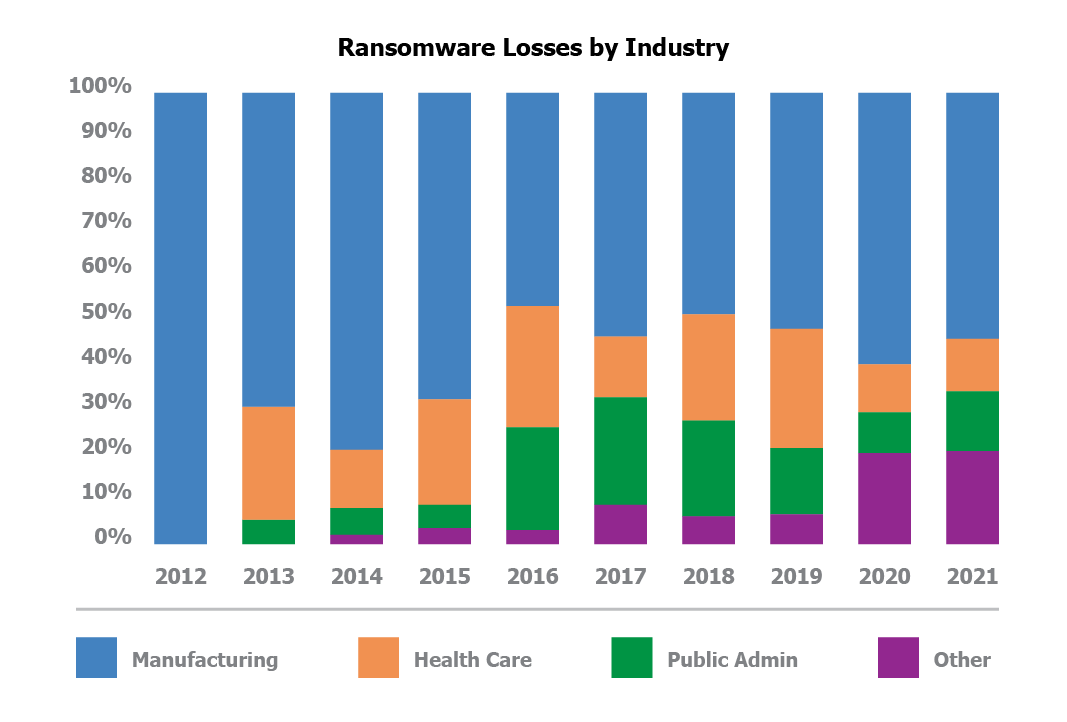
Looking at ransomware losses by industry over time, public administration and health care were some of the most frequently targeted industries from 2013 to 2019; manufacturing accounted for a relatively small percentage of total ransomware attacks. However, by 2020, manufacturing became the most commonly targeted industry.
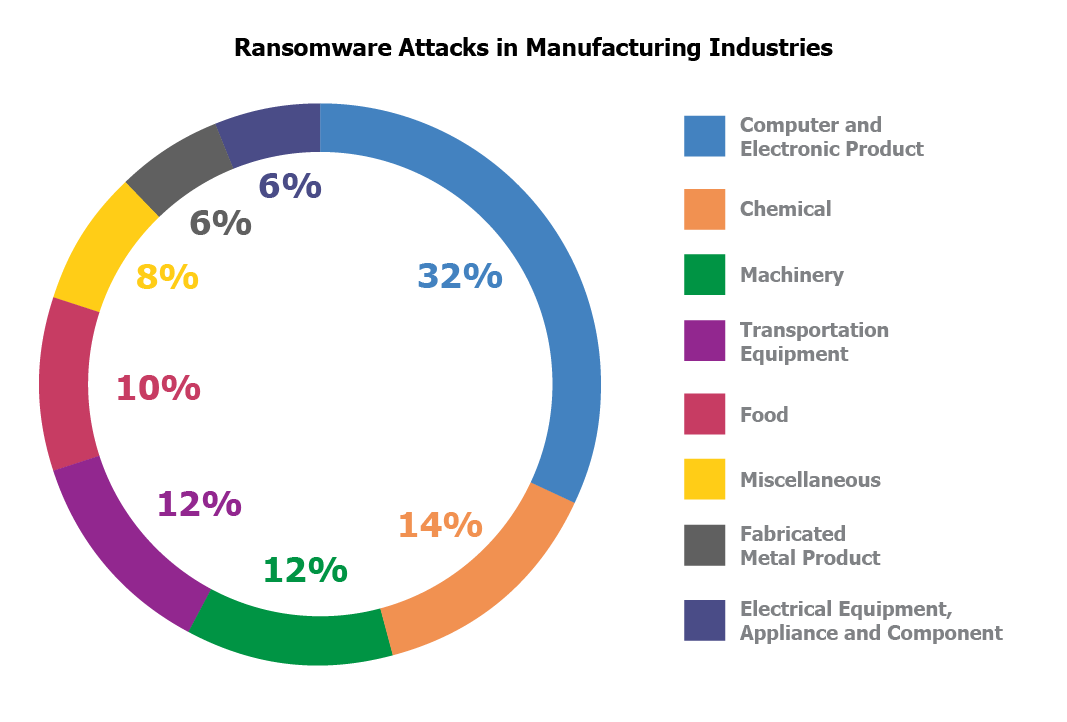
Within the manufacturing industry, computer and electronic product manufacturing saw nearly double the number of ransomware attacks than any other category at 32%. These attacks include ransomware attacks on an Apple supplier, Samsung Electronics and Bose Corporation, according to Advisen loss data.
Chemical manufacturing accounted for 14% of the remaining losses, while machinery manufacturing and transportation equipment manufacturing each accounted for 12%, according to Advisen loss data.
Contact INSURICA today to learn more about our manufacturing industry services and capabilities.
© 2022 Zywave, Inc. All rights reserved.
About the Author
Share This Story
Related Blogs
Making an Acquisition? Why the EMOD Shouldn’t Be Overlooked
When acquiring another company, there’s no shortage of factors to consider. From valuing physical assets to estimating potential synergies, the due diligence process can be complex. However, one critical element often overlooked is the EMOD.
2026 Employer Mandate Update
In July 2025, the IRS released new guidance increasing both the affordability percentage and penalty amounts under the Affordable Care Act’s employer mandate for the 2026 plan year. These changes will affect how Applicable Large Employers (ALEs) determine affordability and assess compliance risk moving into the next benefits cycle.
Facility Rental: Best Practices for Non-School Use
As community hubs, school districts often open their doors to outside organizations for events, activities, and gatherings. This facility rental for non-school use can benefit the community, but it also comes with potential risks. School administrators must take proactive steps to protect district property, reduce liability exposure, and ensure compliance with state laws.